Additive manufacturing, better known as 3D printing, is the modern holy grail of automotive development. When combined with artificial intelligence (AI), it allows an auto company to quickly develop, produce and test parts in a repeating cycle until every available gram of weight or count of wind drag is removed, leaving only what needs to be there.
Supercar maker Czinger Vehicles, based in Los Angeles, was co-founded and is run by Kevin and Lukas Czinger, father and son. Kevin is also CEO of Czinger’s parent company Divergent Technologies, a pioneer in 3D-printing technology. Czinger Vehicles is the direct beneficiary of this innovation, and now other automakers like Aston Martin, Mercedes-AMG and Bugatti are taking a hard look at what Divergent Technologies is doing.
Czinger Vehicles’ first model, called the 21C, was designed by AI and looks appropriately aggressive thanks to an interior and exterior designed by AI.
During Monterey Car Week, Czinger delivered its first customer car at The Quail, A Motorsports Gathering. The 21C Blackbird Edition, inspired by the hypersonic plane of the same name, features a twin-turbocharged, 2.9-liter V8 engine, designed in-house by Czinger. It’s paired with a seven-speed sequential transmission that sends power to the rear wheels only.
The engine delivers 950 horsepower (hp), and when attached to the car’s 800-volt electrical system motors, the total output measures 1,350 hp.
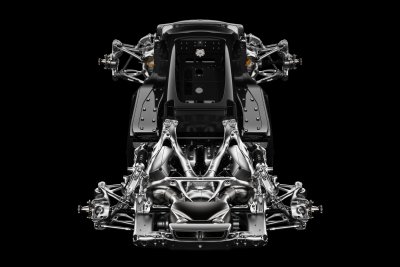
Czinger
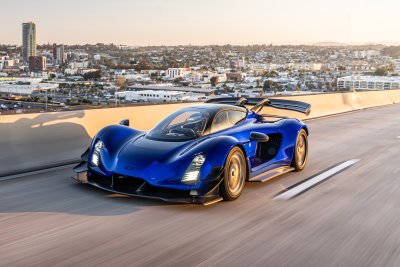
Czinger
Building a handful of bespoke supercars doesn’t prove a 3D-printing manufacturing plan will be successful in the long run.
Divergent Technologies used its Divergent Adaptive Production System (DAPS) to design, engineer, additively manufacture, and assemble chassis and suspension components for Bugatti’s upcoming hypercar, the Tourbillon.
Bugatti said that it tapped Divergent because of its proven experience and because the company is a certified supplier in automotive and aerospace field.
“Bugatti starts with the engineering process, owns the technical specifications like layout, loads, interfaces and manages the integration into the chassis and vehicle. Divergent is responsible for the component shape and does the performance validation (under Bugatti’s direction) as the wing profiled link,” a Bugatti spokesperson told Newsweek.
The system of production enables automakers to design and create vehicle parts constrained only by their imagination, cost and the capabilities of the 3D printer.
DivergentTechnologies’ system eliminates the need for traditional tooling, reducing capital costs.
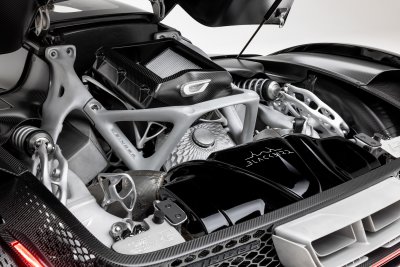
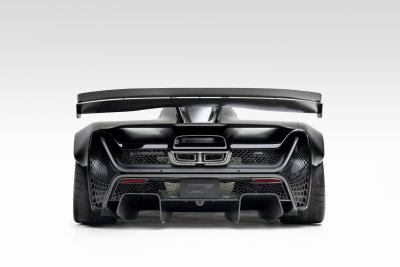
Czinger
“The generative design process optimizes components’ shape and structure, resulting in lighter and stronger parts. This reduction in weight contributes to improved fuel efficiency and performance. Additionally, the flexibility of additive manufacturing allows for rapid design iteration, condensing development times and allowing customers to immediately move designs into high volume production,” a Czinger representative told Newsweek.
The material used is from a family of proprietary aluminum alloys developed in-house by Divergent Technologies. There are no rare-earth or otherwise difficult-to-procure alloying elements. The aluminum alloy powder is melted and fused layer by layer to build the part.
The company says the technology can be used for gasoline or electric vehicles, and that it’s more energy efficient than traditional manufacturing methods because there are no energy-intensive processes like forging or machining.
Additionally, lightweighting the components decreases energy consumption in both gas and electric vehicles once they are in consumer hands.
A 3D Printing Company Bringing Tomorrow to Today
Czinger is uniquely placed to have a major impact on the cars of tomorrow. With financial backing and confidence from some of the world’s leading high-value vehicle makers, they are a company to watch.
So far Divergent Technologies has only built bespoke parts for luxury and hyper luxury customers. The company is working on 3D-printed spare parts and components for various vehicles, from classic models to high-performance cars for Mercedes-AMG, though the company says it hasn’t used Divergent’s parts in a production vehicle yet.
For Aston Martin, Divergent 3D-printed a rear subframe for the limited-edition DBR22 model.
The system can be applied to interior parts as well. The steering column in Czinger’s 21C was 3D printed.
Divergent’s design process comes from original equipment manufacturer (OEM) requirements, such as design volumes, hardpoints, load cases, and stiffness targets. Each design is the expression of those constraints.
Czinger’s footprint is smaller than an average plant, replacing the traditional assembly line with a modular setup (consisting of printers and universal assembly cells), which also makes it flexible, more flexible that what some of the bigger companies can do. Its factory in California is called Area 21 and has a footprint of 50,000 square feet; Nissan’s Smyrna, Tennessee plant, for reference, is 6.4 million square feet.
“Architecting an end-to-end system of this scale and ambition required ground-up innovation and invention of the sort rarely found in today’s incumbent OEMs. Divergent now has over 700 patents covering significant intellectual property white space, creating a meaningful gap for any potential competitor to close,” said Czinger.
Czinger says it sees significant inbound interest from both automotive OEM and aerospace and defense customers.
“Increased use of 3D printed/additive manufacturing can support the challenge of the lightweight design, balancing the increase from hybrid powertrains and other additional features and functions of the vehicles. It can offer unique design, beyond the limits of the standard technologies,” said Bugatti.
👇Follow more 👇
👉 bdphone.com
👉 ultraactivation.com
👉 trainingreferral.com
👉 shaplafood.com
👉 bangladeshi.help
👉 www.forexdhaka.com
👉 uncommunication.com
👉 ultra-sim.com
👉 forexdhaka.com
👉 ultrafxfund.com
👉 ultractivation.com
👉 bdphoneonline.com